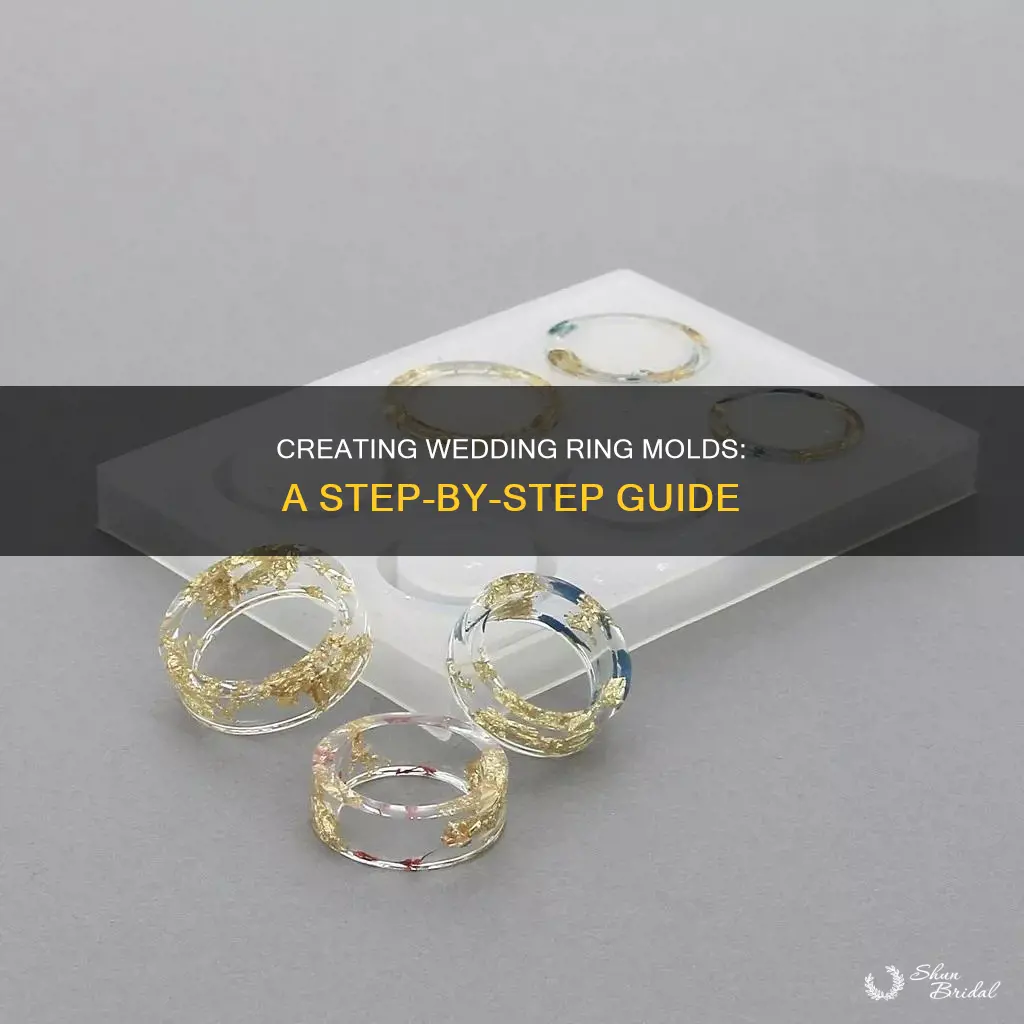
Wedding ring molds can be made from a variety of materials, including silicone, wax, graphite, sand, and plaster. The process of making a wedding ring mold typically involves creating a positive model of the ring, which is then used to create a negative mold. This mold can then be used to cast the final ring in metal or another material.
One common method for creating a wedding ring mold is the lost wax casting method, in which a wax model of the ring is created and embedded in plaster. The plaster is then heated, causing the wax to melt and leave a negative impression in the plaster. Molten metal is then poured into the impression to create the final ring. This method can be used to create detailed and complex ring designs.
Another option for creating a wedding ring mold is to use silicone. Silicone molds are flexible and can be used to create rings in a variety of colors. Silicone molds can also be purchased ready-made from sites like Etsy.
How to Make Wedding Ring Molds
Characteristics | Values |
---|---|
Materials | Wax, Silicone, Plaster of Paris, Metal, Skin Grade 2 Part Silicone, Graphite, Rubber, Sand |
Tools | Melting pot, Stove, Pliers, Paper cup, Hammer, Hacksaw, Dremel tool, Wood files, Sandpaper, CNC router |
Techniques | Lost wax casting, Casting, Molding, Carving, Vibrating, Heating, Melting, Pouring |
Time | 8 minutes to cure silicone, 6 hours to cure ring, 2 weeks to dry plaster, 30 minutes to heat mold, 1 hour to cool metal |
Complexity | Simple shapes are easier to make, reusable molds can be made |
Cost | Custom graphite molds can be expensive |
What You'll Learn
Using wax molds
Wax molds are a great way to make wedding rings, especially if you are replicating an existing design or creating multiple copies. This process is called "lost wax casting". Here is a step-by-step guide on how to make wedding rings using wax molds:
Step 1: Create a Wax Model
First, you will need to create a wax model of your ring design. You can use wax flakes or blocks and melt them into a liquid form. Then, pour the molten wax into a mold to create your desired ring shape. You can use a simple mold, such as a small popcorn tin lid, or get creative and design a more complex shape. If you are replicating an existing ring, you can create a rubber mold by placing the ring in a container with rubber sheets and heating it in a hot press.
Step 2: Prepare the Wax Model
Once your wax model has cooled and hardened, it's time to prepare it for the next steps. If you created a simple mold, you can draw a template on paper and use a carving knife to shape the wax according to your design. If you are using a rubber mold, you will need to cut it open carefully so that it can be closed back tightly when you are ready to make the wax duplicate.
Step 3: Create a Plaster Mold
To create a plaster mold, you will need to attach a small crayon or metal stem to your wax model. This will create an opening for the metal to be poured in later. Then, place your wax model on a paper cup and melt some crayon onto the bottom to create a pedestal. Mix a batch of plaster and pour it into the cup, tapping it to remove any air bubbles. Allow the plaster to dry completely, which may take a couple of weeks.
Step 4: Remove the Wax
Before you can pour metal into your plaster mold, you need to remove the wax. Heat the mold in a furnace or oven for about 30 minutes to melt the wax, and then let it cool. Break open the mold and remove the wax, leaving a negative impression of your ring design.
Step 5: Cast the Ring
Now it's time to turn your wax model into a metal ring. Melt your chosen metal (such as gold or platinum) in a crucible or melting pot and pour it into the opening of your plaster mold. Allow the metal to cool completely before breaking open the mold and removing your ring.
Step 6: Finishing Touches
Finally, it's time to add the finishing touches to your ring. Cut off any excess metal, file down rough edges, and polish your ring to a shine. You can use sandpaper to smooth out any imperfections and create a mirror-like finish.
Creating wedding rings using wax molds is a detailed process that requires patience and creativity. With the right tools and techniques, you can design and craft your own unique wedding rings.
The Perfect Wedding Hair Updo: A Step-by-Step Guide
You may want to see also
Casting metal rings
To cast a metal ring, you will need the following materials:
- Wax for carving the ring model
- Heat-resistant cementing material, such as plaster of Paris
- Metal of your choice (e.g., zinc, silver, gold)
- Crucible for melting the metal
- Centrifuge or sling for casting
- Safety gear, including gloves and protective glasses
Step 1: Carve the Wax Model
Begin by carving your ring design out of wax. You can use different types of wax depending on the desired outcome. Softer sculpture wax can be shaped like clay, while harder waxes can be used to achieve textures in the final piece. Draw a template on paper to guide your carving, and use a compass to create smooth curves if needed. You can also trace a normal wedding ring to get the correct size.
Step 2: Prepare the Mould
Attach sprues (small wax rods) to your wax model and weigh it. The sprues will be used to create a channel for pouring the metal later. Melt some wax onto the base of your flask (a small container for holding the mould) and attach the wax model. Mix investment powder (a heat-resistant cementing material) with water in a ratio determined by the weight of your wax model. Place the investment mixture in a vacuum chamber to remove air bubbles, then pour it into the flask and let it dry overnight.
Step 3: Burn Out the Wax
Place your flask in a kiln to burn out the wax. The timing and temperature will depend on the size of your flask. After heating, remove the flask from the kiln and place it on a bed of gravel or sand to cool. The wax should have melted out, leaving a cavity in the mould for the metal.
Step 4: Melt the Metal
Melt your chosen metal in a crucible. You can use a dual-gas torch or a kiln to heat the metal until it is molten. Be sure to wear safety gear to protect yourself from the heat and any fumes. Once the metal is molten, skim off any slag or impurities that may have formed on the surface.
Step 5: Cast the Ring
Place your flask in the cradle of the centrifuge or sling and lock it into place. Preheat the crucible, then pour the molten metal into it. Use the centrifuge or sling to force the molten metal into the mould through the sprue channels. This will ensure that the metal fills all the details of the ring design.
Step 6: Remove the Ring from the Mould
Allow the metal to cool until it is no longer glowing red. Then, remove the flask from the centrifuge and submerge it in a bucket of water to quench the metal. Break open the mould and scrape out any remaining investment material. Cut off the sprues and use a hacksaw or file to remove any rough edges.
Step 7: Finishing
Sand and polish your ring to achieve the desired shine and smoothness. You can use sandpaper cut into strips to rub the ring to a shine. Finer grits of sandpaper will give you a smoother finish. Finally, buff the ring with an old shirt to give it a mirror finish.
Get Glowing Skin for Your Wedding Day
You may want to see also
Making silicone molds
Making silicone moulds for wedding rings is a simple process that can be done at home. Here is a step-by-step guide:
Materials
To make silicone wedding rings, you will need skin-grade 2-part silicone, gel-based food dye, and two ring moulds. It is important to use skin-grade silicone to ensure it is safe for extended periods on your hand. Gel-based food dye is also essential, as normal liquid dye will not mix well with the silicone.
Mixing the Silicone and Dye
Following the instructions on the bottles, mix the 2-part silicone with a 1-to-1 ratio. Stir the mixture thoroughly for about a minute. Then, add a couple of drops of your chosen gel-based food dye and stir until it is fully combined. You can create different colours by adjusting the amount and type of dye added.
Pouring the Silicone into Moulds
The silicone starts to cure and set after around 8 minutes, so you will need to work quickly. Carefully pour the coloured silicone into your ring moulds, using a stick to ensure it reaches all the way to the bottom and remove any air bubbles. Air bubbles can weaken the structure of the ring, so it is important to remove as many as possible. You can use a vacuum chamber for this, or simply drop the moulds down hard to bring the bubbles to the top. Wipe off any excess silicone to ensure the ring is smooth and level.
Removing the Rings from the Moulds
Place the moulds on a flat surface and wait for at least 6 hours for the silicone to fully cure. Removing the rings from the moulds can be challenging, especially if you have not used any mould release or oil. You may need to turn the moulds inside out to pull the rings free.
With these simple steps, you can create your own unique and colourful silicone wedding rings. You can experiment with different colours, or even make clear rings by omitting the dye. This method is a cheap and easy way to make custom rings that are perfect for everyday wear or as a backup to your metal wedding band.
Crafting Memorable Wedding Speeches: A Guide to Perfection
You may want to see also
Using a CNC router for custom graphite molds
Using a CNC router for custom graphite moulds is a great way to make wedding rings, but it does come with some limitations.
Firstly, you can pay to have custom graphite moulds made, or you can make them yourself if you have access to a CNC router. There are makerspaces that can help you with this. However, creating complex shapes will be challenging and expensive, so for simpler shapes, it may be better to order the metal and work with that directly.
If you do decide to use a CNC router, you will need to consider the dust created by cutting the graphite. Graphite dust is nasty and will get everywhere, so you will need a dust collector and a vacuum collection system to prevent it from getting into the machine's internals and causing damage. You will also need to be prepared for increased maintenance costs and a shorter lifespan for your CNC router.
CNC machines are great for creating wax master models for casting, as they can produce more complex and precise geometries than hand-carved pieces. They are also faster, but you will need a CAD file of your ring design. To avoid the wax warping during the milling process, you will need a machine with a special cooling system.
Overall, while using a CNC router for custom graphite moulds for wedding rings is possible, there are some important considerations and limitations to this method.
Crafting a Heartfelt Wedding Anniversary Card for Your Wife
You may want to see also
Sand casting
Step 1: Pattern & Core Making
Create a pattern, which is a replica of the desired casting, in the sand. This can be done using wooden, plastic, or metal patterns to create the mould cavity. Sand cores are also formed during this step to create internal features like holes. This step requires careful consideration of various factors, such as pattern material, geometry, withdrawal method, distortion, and shrinkage.
Step 2: Mold Preparation
The second step involves creating a mould using different types of sand, additives, binders, and water. There are two main methods for mould preparation: hand moulding and machine moulding. Hand moulding is a manual process, while machine moulding involves the automated creation of green sand moulds.
Step 3: Melting & Pouring
In this step, the metal is melted in a furnace, such as an electric arc or induction furnace. Once molten, the metal is carefully poured into the mould.
Step 4: Solidification & Cooling
The molten metal solidifies and cools in the mould, potentially with the use of a riser to feed material. Controlled cooling is essential to ensure the proper structure of the casting.
Step 5: Shakeout & Cleaning
The mould is broken, and the casting is removed. The gating system, which guides the molten metal into the mould cavity, is cut off. The casting is then cleaned using methods like sandblasting to remove any residual sand or debris.
Step 6: Inspection & Finishing
The final step involves inspecting the casting for any defects and applying finishing touches. This includes visual inspection, magnetic testing, ultrasonic testing, and metallurgical control. Secondary manufacturing processes, such as grinding, turning, or welding, may be applied to enhance the final product.
Creating Beautiful Flower Cones for Your Wedding Day
You may want to see also
Frequently asked questions
There are several methods for making wedding ring moulds, including casting from a mould, using a CNC router, or creating a silicone mould. The best method for you will depend on your specific needs and requirements.
Materials such as silicone, wax, plaster, rubber, and metal can be used to make wedding ring moulds. The choice of material will depend on the specific method and the desired outcome.
To make a silicone wedding ring, you will need skin-grade 2-part silicone and gel-based food dye. Mix the silicone in a 1-to-1 ratio, add your desired colour of dye, and stir thoroughly. Work quickly, as the silicone will start to cure after about 8 minutes. Pour the mixture into your ring moulds and use a stick to remove any air bubbles. Allow the silicone to cure for about 6 hours before removing the rings from the moulds.
The lost wax casting method involves creating a wax positive of the final product, which is then embedded in plaster. The plaster is heated, causing the wax to melt and leave a negative impression. Molten metal is then poured into the impression to create the ring.