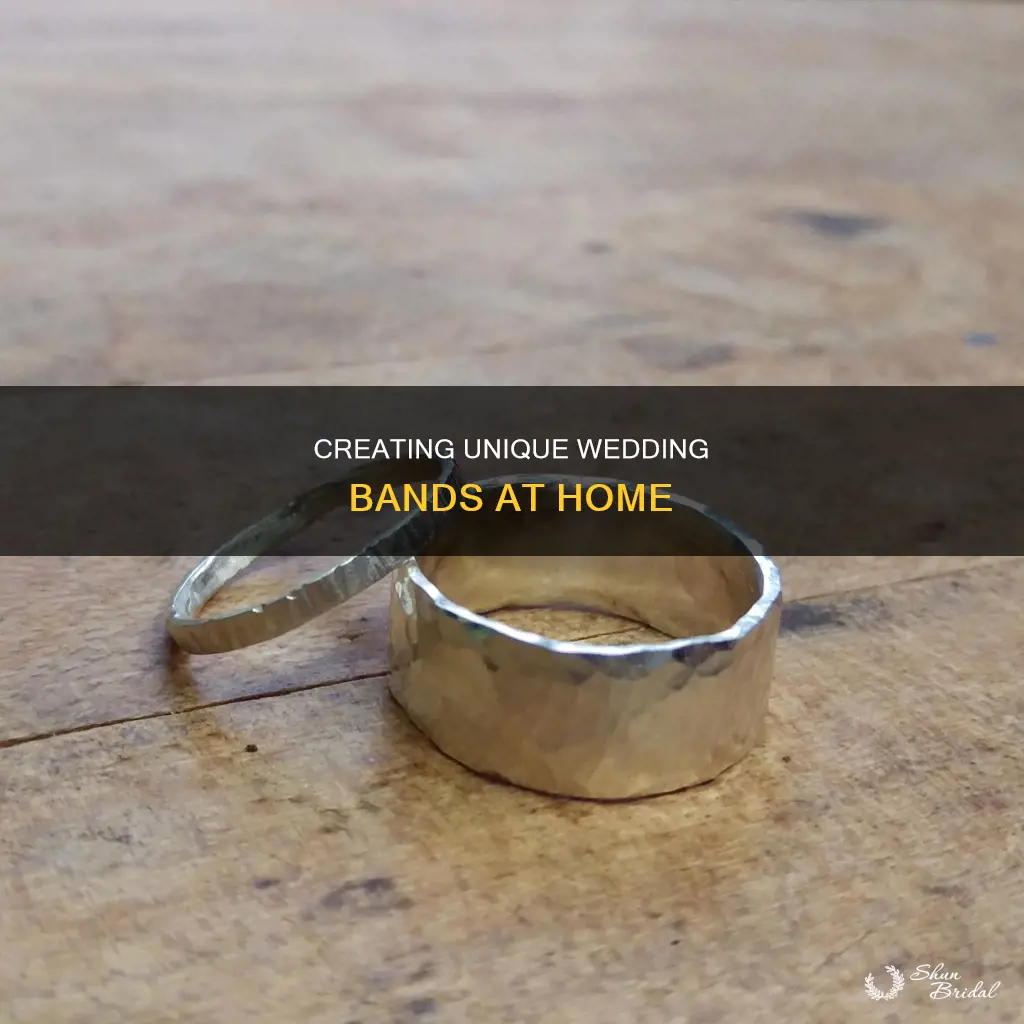
Making your own wedding bands is a unique and memorable experience that allows you to create one-of-a-kind rings imbued with your love and memories. Through private or group workshops, couples can work with professional artists and instructors to design and craft their own wedding bands, often in a single day. These workshops cater to all skill levels, offering guided instruction in various jewellery-making techniques such as wax carving, casting, fabrication, and polishing. With a range of materials to choose from, including gold, silver, and recycled metals, couples can create classic, timeless, or personalised designs, adding textures, finishes, and even custom inscriptions. The cost of these workshops typically includes instruction, materials, and sometimes additional perks like lunch, photos, and a bottle of bubbly to celebrate.
Characteristics | Values |
---|---|
Time | 2-7 hours |
Location | Various locations across the US |
Cost | $625-$1,900 |
Materials | Sterling silver, 10k or 14k yellow, white or rose gold |
Tools | Hammers, torches, wire stock |
Techniques | Wax carving, casting, fabrication |
Design | Textured surfaces, matte, brushed or polished finishes, stamped inscriptions |
What You'll Learn
Picking stones, metal and sizing
Picking the perfect stones, metal and sizing is an important part of the ring-making process. Firstly, you need to decide on the type of metal you want for your wedding bands. Popular choices include sterling silver, 10k or 14k yellow, white or rose gold, and platinum. The cost of the metal will depend on the current market price and the size and width of the ring. For example, a wider ring for a larger finger will have a higher cost than a thin band for a smaller finger. You can also choose to add a soft general curve to narrow bands to accommodate some engagement ring styles.
Next, you can decide if you want to add any stones to your wedding bands. Small flush-set diamonds, moissanites or sapphires can be a beautiful addition. Keep in mind that adding stones will incur additional charges and may require more time for setting. If you're looking for a more complex design with individual settings, you may need to consult a professional jeweller, as this is an advanced skill.
Finally, sizing is a crucial aspect of ensuring your wedding bands are comfortable and fit perfectly. The width and thickness of the band can impact the sizing, so it's important to consider this in conjunction with the desired metal and stone choices. Most workshops will provide guidance on how to measure your finger accurately to determine the correct size. It's also worth asking about their resizing policy in case any adjustments are needed after the rings are made.
Creating a Homemade Wedding Canopy: A Step-by-Step Guide
You may want to see also
Wax carving
To begin the carving process, you'll need to measure the width of the ring and mark it on the wax tube using a divider. Then, you'll saw off the desired width and file down any rough edges to create a smooth surface. This process ensures that the sides of the wax are flat and parallel, which is crucial for accurate marking and measuring.
The next step is to enlarge the hole to the appropriate finger size. This is done using a ring sizer with a blade, allowing you to adjust the size by removing material from the inside of the ring. After achieving the desired size, you can further refine the design by filing and carving the wax into the desired shape. If you're creating a half-round band, for example, you'll file a bevel and then soften the edges by connecting the bevels to form a smooth, round finish.
It is important to smooth out the surface of the wax model to minimise the amount of work needed once the ring is cast in metal. This can be achieved using sandpaper or a nylon stocking. Additionally, rounding the edges of the band and ensuring that the ring looks proportional from all angles are crucial steps.
For a more intricate design, you can use a set of calipers to mark measurements around the wax for the profile of the ring. This will guide you in trimming away excess wax and shaping the band. Finally, you can add beads to the wax model, which will eventually hold the diamond or gemstone in place. These beads are melted into place using a warm wax tool, completing the wax model and preparing it for casting.
Creating Fondant Wedding Cake Decorations: A Step-by-Step Guide
You may want to see also
Casting vs fabricating
When it comes to making homemade wedding bands, there are two main production methods: casting and hand fabrication. Both methods have their own advantages and disadvantages, and the best choice depends on the specific design and requirements of the ring.
Casting is the process of pouring molten metal into a mould to create the desired shape. This method is commonly used by retailers due to its efficiency and lower cost compared to handmade jewellery. It involves creating a wax model of the final product, which is then covered in plaster and heated to create the mould. While casting can produce precise results using digital renderings and 3D printing, there is a risk of porosity (small air pockets within the metal) that can weaken the structure. Cast metal is also less dense and more prone to scratching and bending. Creating intricate designs with multiple types of metal can be challenging, as each component must be cast separately and then soldered together.
Hand fabrication, on the other hand, involves working with metal from scratch using a high level of craftsmanship. This process starts with raw pieces of metal, typically in the form of wire or sheets, which are then cut, hammered, shaped, and annealed (heated) to create the desired design. Hand-fabricated jewellery is denser and more durable than cast jewellery, making it less susceptible to scratching and bending. It allows for finer and narrower designs with a more delicate appearance and easier mixing of different metals in a single piece. However, hand fabrication is more time and labour-intensive, resulting in higher costs.
For unique and intricate designs, casting may be a preferred choice, while hand fabrication is ideal for creating high-quality, durable pieces with a more refined appearance. When deciding between casting and fabricating homemade wedding bands, consider factors such as complexity of design, desired level of durability, and budget.
Creating Illusion: Fake Wedding Cake Tiers
You may want to see also
Hammering and texturing
To begin hammering and texturing, you will need a hammer and a metal ring band. Place the band on a hard, flat surface, such as an anvil or a sturdy workbench. Hold the band firmly in place with one hand, and use the other hand to hammer it. You can use a variety of hammers, from a standard metalworking hammer to a specialised jewellery hammer with different head shapes to create unique textures.
When hammering, strike the band with deliberate, controlled force. You can create different textures by varying the force and angle of your strikes. For example, light taps with a ball-peen hammer can create a dimpled texture, while stronger blows with a chasing hammer can leave deep, angular grooves. Experiment with different hammers and techniques to find the style that suits your taste.
In addition to hammering, you can also use other tools to create textures. Files, chisels, and punches can be used to create lines, cross-hatch patterns, or other intricate designs. If you want to add further detail, you can use metal stamps to imprint letters, numbers, or symbols onto the band. This is a great way to include a personal message, the wedding date, or the couple's initials.
The hammering and texturing process allows couples to be creative and add their unique mark to their wedding bands. It is a fun and satisfying step in the ring-making process, resulting in a one-of-a-kind ring that symbolises the love and commitment between two people.
Creating Heartfelt Wedding Anniversary Greeting Cards at Home
You may want to see also
Polishing
Once you have cast your wedding bands, the next step is to polish them. Polishing is the process of smoothing out the surface of the metal to create a shiny finish. There are several ways to polish your wedding bands at home, depending on the materials you have available.
Using a Burnishing Tool
One method of polishing is called "burnishing", which involves using a smooth stainless steel implement to smooth out the metal without removing any of it. This can be done with any smooth stainless steel object, such as a screwdriver or the back of a spoon. Simply rub the steel implement over the surface of the ring for about 10 minutes, and then finish with a polishing cloth. This method is suitable for platinum and gold rings.
Sandblasting
Another option for polishing your wedding bands is to use a process called sandblasting. This involves using a media blaster to blast the ring with sand or other media, which smooths out the surface. This method can be more aggressive than burnishing and may remove some metal, so it is important to be careful not to overdo it.
You can also use polishing compounds to smooth out the surfaces of your wedding bands. This involves using small polishing wheels or pads along with a polishing compound, such as Fabulustre, to create a shiny finish. This method may require more time and effort than the previous two methods, but it can be effective in achieving a high shine.
Professional Polishing
If you are unsure about polishing your wedding bands at home, you can always take them to a professional jeweller to have them polished. Professional jewellers have access to specialised equipment and techniques that can ensure a high-quality polish. However, keep in mind that professional polishing may remove some metal from your ring, so it should not be done too frequently.
Creating Orthodox Wedding Crowns: A Step-by-Step Guide
You may want to see also
Frequently asked questions
The rings can be classic, minimal, and timeless designs with textured surfaces made using hammers and other tools. They can be finished with matte, brushed, or polished surfaces and may include custom personalization through stamped inscriptions.
The materials available include 14K and 18K Yellow Gold, 14K Rose Gold, 14K and 18K Palladium White Gold, and sterling silver. The cost of the rings will depend on the materials used, the ring size, and the width of the band.
No prior experience is necessary. You will receive guided one-on-one instruction from a professional artist or an experienced instructor, who will teach you the necessary techniques.
The time taken can vary depending on the couple's pace and the complexity of the design. On average, it can take around 2-7 hours to complete the rings, with some workshops offering fabrication methods that can be faster, taking around 4 hours.
Yes, most workshops offer complimentary ring resizing within a certain period after the workshop. If additional material is required for resizing, there may be an additional cost.