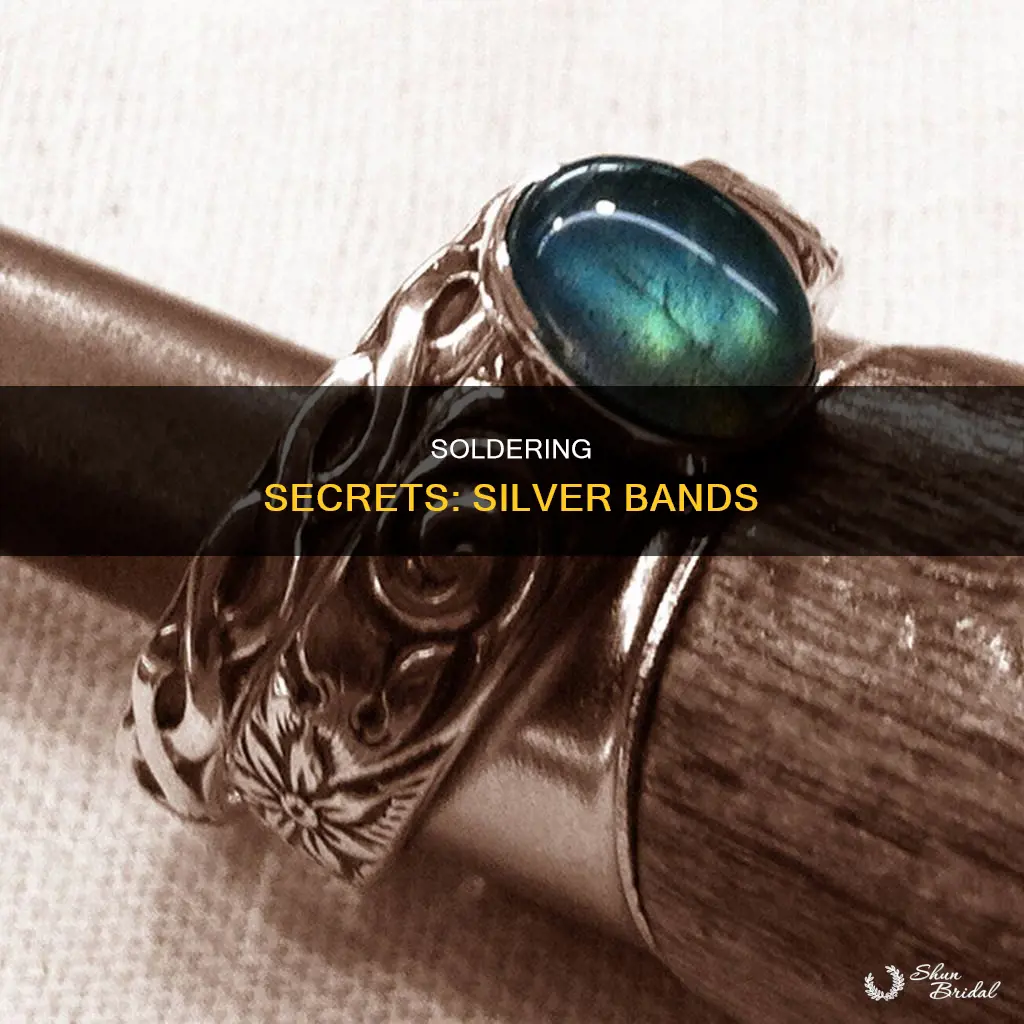
Soldering silver wedding bands is a popular choice for brides who want to create a bridal set that connects the metals of both bands together. Soldering is the process of fusing two rings together to form one, using a filler metal that is melted to bond the rings without altering or damaging them. This technique can be used to join an engagement ring and a wedding band, reducing wear and tear caused by friction and creating a more comfortable fit. However, it is important to consider the cons of soldering, such as the inability to wear the rings separately and the potential damage to the rings if they are separated later.
Characteristics | Values |
---|---|
Soldering process | Fusing two rings together to form one bridal set |
Metals used | Filler metal |
Ring alteration | Rings themselves are not altered or damaged |
Ring maintenance | Less maintenance, more money saved in the long run |
Ring movement | No more sliding around, spinning or thrashing around |
Comfort | More comfortable fit, no skin irritation or pinching |
Ring alignment | Rings will always line up perfectly |
Wearing options | Unable to wear just one ring, must wear both at all times |
Versatility | Unable to mix and match with other bands |
Ring separation | Rings are difficult to separate, risk of damage |
Ring resizing | May need to size up by a quarter |
Timeframe | Takes about 1-2 weeks |
What You'll Learn
Choosing the right solder
Metal Composition
The type of metal used in the solder is crucial. For silver wedding bands, a common choice is to use a solder made from sterling silver, which is an alloy composed of 92.5% pure silver and 7.5% copper. This composition provides a good balance between durability and workability.
Durability
When selecting a solder, consider the durability of the joint it will create. Solders with higher silver content tend to be softer and less durable, while those with additional metals like palladium or other precious metals can increase the strength and integrity of the joint. Palladium sterling silver, for example, offers higher durability due to the inclusion of palladium, a member of the platinum family.
Ease of Soldering
Some solders are easier to work with than others. For instance, sterling silver is known for being easy to solder, making it a popular choice for those creating their own wedding bands. It's essential to choose a solder that suits your skill level and the equipment you have access to.
Finish
The solder you choose should complement the finish of your silver wedding band. Silver is versatile and can be finished in various ways, from bright white to oxidized black and high polish to soft satin. Ensure the solder you select will create a seamless joint that matches the desired finish of your ring.
Cost
Cost is an important consideration when choosing a solder. Solders containing precious metals like palladium or gold can be more expensive. If you're on a budget, opt for a standard sterling silver solder or consider other silver alloys with additional metals that enhance durability without significantly increasing the price.
Remember, selecting the right solder for your silver wedding band project is crucial to achieving a secure and aesthetically pleasing joint. Consider the metal composition, durability, ease of soldering, finish, and cost to make an informed decision.
Wedding Bands: Payment Options
You may want to see also
Preparing the silver band
The first step in preparing a silver band for soldering is to choose the stock. You can use either sheet or wire, with the benefit of wire being that it gives an instant shape, such as half-round wire or square wire. The benefit of using a sheet is that it is much easier to work with than wire. For a beginner, it is recommended to use an 18 gauge (1 mm) or 16 gauge (1.3 mm) sheet.
The next step is to cut the ring blank. You can use a slide gauge or dividers to score a cut line, and then cut using a guillotine or long arm metal shear. Alternatively, a jeweller's hand saw can be used, which also provides an opportunity to improve your sawing skills. Don't worry if the cut job is not perfectly straight or parallel, as this can be easily fixed later in the process.
If you used a long arm metal shear, the next step is to straighten the ring blank, as this tool will always put a curve in the blank. Anneal the sterling silver using a steel block and a rawhide hammer. Remember that steel is harder than sterling silver and can easily damage it, so be careful not to use too much force when straightening.
The next step is to file the first side of the joint. This is where a "V" board comes in handy, as it is designed to support you while you work. You can modify the "V" board with grooves to offer further support. File one end of the ring blank 90 degrees to the long edge using a hand file.
Now it's time to measure the ring blank. There are various ways to do this accurately, including using a ring blank chart. Place the filed end at the "start" point and mark the metal with a sharpie at the appropriate ring size.
The next step is to cut and file the second side of the joint. Use a jeweller's hand saw to cut the ring blank down to the required size, and then repeat the filing process on the other side of the joint. Both sides of the joint should now be filed at a 90-degree angle to the long edges, and the ring blank should be the correct length.
At this point, you can start bringing the joint together. Using your hands or soft-tipped pliers, bend the ring blank into a wide "U" shape and then into a wide "teardrop" shape. Use a rawhide or soft hammer and a steel block to hammer straight down on the ring blank until it resembles the shape of a Hershey's Kiss. Continue hammering and adjusting until both ends of the joint are laying flat with little or no gap between them.
There will likely be a gap between the joint, and the edges may not touch in some points. A bad practice is to fill joints with solder, as this will result in a different colour than the rest of the ring. Instead, use a jeweller's hand saw to cut down the middle of the joint, taking care to hold the ring firmly to avoid movement. Cut right down the middle, removing a little material from both sides. This step may require multiple passes to remove enough material to close the gap.
Now it's time to solder the ring. Apply liberal amounts of flux all around the seam using a paintbrush. Solder comes in sheet or wire form, and it is recommended to use wire as it is easier to cut. When soldering, use as little solder as possible, as any extra solder will need to be filed or sanded off later. Cut multiple small pieces (about 2 or 3 mm long) and place the solder at the beginning of the seam.
Use a medium-sized flame to heat the ring evenly in a circular motion. First, the flux will boil, then turn chalky white, and finally, clear. At this point, place the solder and use a titanium pick to move it around. Ball up the solder by placing the torch directly over it, and then use the pick to scoop it up. Place the solder on the top edge of the seam and gently brush it off the pick. If the solder is not in the middle of the seam, gently nudge it into place with the pick.
Heat the ring evenly until there is a slight red glow, and then move the flame to the bottom inside seam. Allow the metal to cool and then pickle for 8 minutes. If the solder did not go all the way through the seam, simply repeat the process.
The final step in preparing the silver band is to clean the solder seam of any excess solder. Use a flat needle file to remove the extra solder before shaping the ring. Be careful not to thin the edges of the ring while removing the excess solder.
Wedding Band Width: Finding the Perfect Fit
You may want to see also
Soldering the ring
Soldering a wedding band is a big decision, as it will likely be worn forever. It is a process of fusing two rings together to form one bridal set. It is a popular choice for brides who want to bond their wedding band and engagement ring together.
Before soldering, it is important to consider the pros and cons of the process. Soldering your wedding band will prevent your rings from sliding around and will preserve the metal, reducing the need for maintenance. It will also create a more comfortable fit, as the rings will move as one, and you won't experience the uncomfortable pinching sensation between the two rings.
However, soldering means you will always have to wear both rings together, and you will lose the versatility of mixing and matching your bands. Additionally, if you decide to separate the rings later, there is a risk of damaging them.
If you decide to go ahead with soldering your wedding band, the process involves melting a filler metal to bond the two rings together without altering or damaging them. It is best to consult a professional jeweller to perform this process, which typically costs around $45.
- Cut the ring blank using a slide gauge or dividers to score a cut line.
- Straighten the ring blank if necessary, using a steel block and a rawhide hammer.
- File the first side of the joint at a 90-degree angle to the long edge.
- Measure the ring blank accurately using a ring blank chart.
- Cut and file the second side of the joint, ensuring both sides are filed at a 90-degree angle.
- Bring the joint together by bending the ring blank into a "U" shape and then into a "teardrop" shape.
- Hammer the ring blank until it resembles the shape of a "Hershey's Kiss".
- Continue hammering and using soft-tipped pliers to align the two joints until there is little to no gap between them.
- Apply flux all around the seam to keep the metal clean while heating.
- Heat the metal evenly until the flux turns clear, indicating it is ready for soldering.
- Place the solder at the beginning of the seam and use a titanium pick to move it into place.
- Heat the ring evenly again until there is a slight red glow.
- Pickle the ring for 8 minutes to ensure the metal is fully cleaned.
- Repeat the soldering process if necessary, ensuring the seam is clean.
- Clean any excess solder from the inside of the ring, being careful not to thin the edges.
- Shape the ring on a steel ring mandrel with a soft hammer.
- Emery and polish the outside and edges of the ring to create a bright and clear finish.
- Hammer texture the ring to create your desired texture and design.
- Emery and polish the inside of the ring to ensure a comfortable fit and remove any scratches or dents.
Sparkle Your Silver Band: A Cleaning Guide
You may want to see also
Finishing the ring
Once you have soldered your silver wedding band, there are a few steps you can take to finish the ring and ensure it is comfortable and durable. Here are some detailed instructions on how to finish a silver ring:
Clean the Solder Seam
Firstly, check that the solder has flowed all around and through the seam. Then, use a flat needle file to remove any excess solder from the seam before shaping the ring. Be careful not to thin the edges of the ring while removing the excess solder.
Shape the Ring
Place the ring on a steel ring mandrel and use a soft hammer to shape it. The mandrel will help you achieve a smooth and round shape without any wobbles. Remember to tap the ring gently and work your way around to avoid creating dents.
Clean Up: Outside Surface of Ring
Use emery sticks to clean and smooth the outside surface of the ring. Be careful not to scratch the metal and avoid fixating on one spot to prevent thinning the metal. Rotate the ring and use a bending wrist to cover as much of the length as possible.
Clean Up: Ring Edge
Use emery sticks to smooth and even the edges of the ring. If one edge is higher than the other, use a flat hand file to file it down. You can also use dividers to score a parallel line and guide your filing.
Polish the Ring
Polish the outside and edges of the ring using a polishing lathe or an alternative rotary tool. Achieve a bright and clear polish before adding any textures to the ring. Remember that scratches and dents cannot be hidden with a texture, so take your time with this step.
Hammer Texturing (Optional)
If you wish to add a hammer texture to your ring, place it back on the steel mandrel and use a hammer to strike the ring. This will cause the metal to stretch and thin, so be mindful of how hard you strike. You can create various textures by using different types of hammers.
Emery and Polish the Inside of the Ring
Use emery sticks to smooth the inside of the ring, removing any dents, scratches, or excess solder. Then, polish the inside to a bright finish using a polishing lathe or rotary tool. It is important to finish the inside of the ring well, as it will be in direct contact with the skin.
Tamar Braxton's Wedding Band Inscription
You may want to see also
Caring for your ring
Now that you have your dream ring, you'll want to keep it looking its best for years to come. Here are some tips to care for your silver wedding band:
Keep it dry: Avoid wearing your ring when showering or swimming, as water can contain chemicals and substances that can tarnish the silver. It's also best to remove your ring when using products like lotion, makeup, or perfume, as these can damage the metal.
Avoid harsh chemicals: The chemicals in cleaning products and even hand sanitiser can be harsh on your ring, so it's best to take it off when doing any household chores or outdoor work.
Be gentle: Diamonds may be one of the hardest materials on Earth, but they can still chip if struck at the right angle. Avoid wearing your ring during any high-impact activities, and be careful not to knock it against other hard materials.
Clean regularly: Use warm water and a soft toothbrush to gently clean your ring at home. Avoid cleaning it over a sink or drain, as you don't want it to slip down the drain! You can also take it to a jeweller for a professional cleaning.
Store it properly: Keep your ring in a separate, soft compartment or container when you're not wearing it. Avoid ring holders or dishes that stack rings on top of each other, as this can cause scratches.
Get check-ups: Take your ring to a jeweller at least once a year for an inspection and cleaning. They can check for any loose settings, worn prongs, or other potential issues.
Insure it: Accidents happen, so it's a good idea to get insurance coverage for your ring in case of theft, loss, or damage. That way, you can rest easy knowing your ring is protected.
Custom Wedding Bands: Where to Shop
You may want to see also
Frequently asked questions
Soldering your wedding band can help to prevent wear and tear on your ring caused by friction between two different metal rings. It will also ensure that your rings stay in place and don't slide around on your finger, providing a more comfortable fit.
Yes, once your rings are soldered together, you will always have to wear them together. This may be inconvenient if you work in a field that requires you to remove your rings frequently or if you like to mix and match your jewellery.
To solder a silver wedding band, you will need to shape, file, saw, fit joints, and finish the ring. This process requires specialised tools and jewellery-making skills, so it is recommended that you seek the help of a professional jeweller.