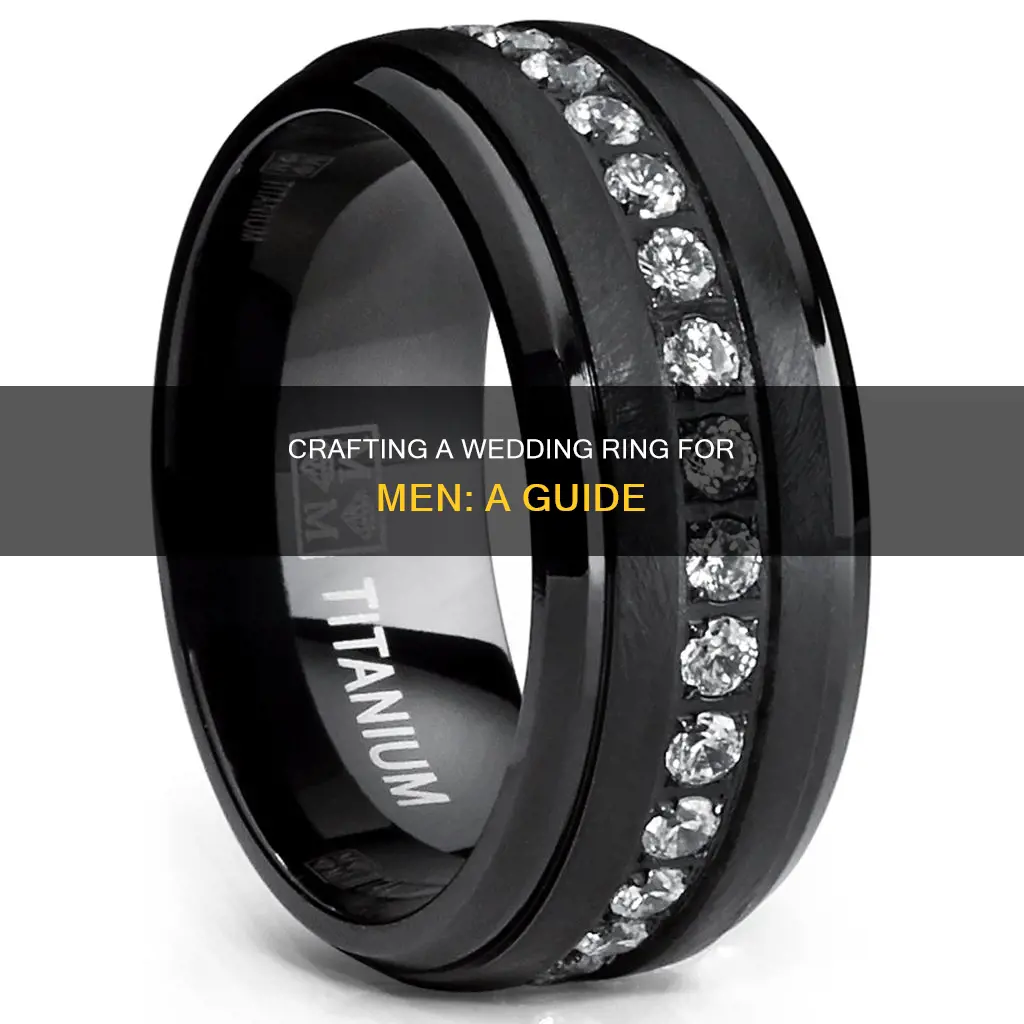
Making a wedding ring for your partner is a thoughtful way to show your love and commitment. Whether you're looking to create a classic design or something more unique, crafting a ring yourself can be a meaningful and enjoyable experience. From traditional metals like gold, platinum, and tungsten to unconventional choices like wood, steel, or even meteorite, the possibilities are endless. You can opt for a DIY approach with the help of online tutorials or attend a wedding band workshop, where you'll work with a professional artist to bring your vision to life.
Characteristics | Values |
---|---|
Materials | Wood, Platinum, Gold, Palladium White Gold, Diamond, Tungsten, Titanium, Tantalum, Cobalt, Silver, Gray |
Design | Classic, Minimal, Timeless, Textured, Matte, Brushed, Polished, Beveled Edge, Beveled Corners, Sanded, Hammered, Comfort Fit, Two-Tone, Natural or Lab-Grown Diamond, Black, Rose Gold |
Cost | $725 workshop fee + ring fee (varies) |
Time | 3-6 hours for basic rings |
What You'll Learn
Choosing the right materials
Gold
Gold is a classic choice for wedding rings and is available in different colours such as yellow, white, and rose gold. When opting for gold, you can choose between different karats, such as 14K or 18K. Gold is a durable and hypoallergenic metal, making it a suitable option for those with sensitive skin. It is also possible to create textured surfaces and add stamped inscriptions to gold rings.
Platinum
Platinum is another popular option for wedding rings. It is a durable and hypoallergenic metal that is often paired with other metals such as 18K yellow gold. Platinum rings can be matte, brushed, or polished to create different looks. Keep in mind that platinum is generally more expensive than gold.
Tungsten
Tungsten is a modern choice for male wedding rings, known for its durability and unique look. It is available in different colours, including classic gray and black. Tungsten rings often feature comfort-fit designs, making them lightweight and easy to wear. This metal is also suitable for those seeking a budget-friendly option, as it is often more affordable than gold or platinum.
Titanium
Titanium is another alternative metal that is lightweight and durable. It is hypoallergenic and available in various colours, including black. Titanium rings are often chosen for their modern aesthetic and affordability.
Other Metals
In addition to the metals mentioned above, you can also explore options such as tantalum, cobalt, or silver. Each metal has its unique style and durability, so it is essential to consider your personal preferences and budget.
Wooden Rings
For a truly unique and masculine ring, you may also consider using wood. Wooden rings are handcrafted and allow for personalisation. When choosing wood, select a dense and strong type, such as African Padauk or Ipe, to ensure the ring's durability. Wooden rings can be sanded, heat-treated, and coated with oil for a smooth finish.
Create Birdseed Wedding Favors with These Easy Steps
You may want to see also
Selecting the correct tools
If you plan to make a wooden ring, you will need a saw to cut the wood to size. A hacksaw, scroll saw, or band saw will all work well for this task. You will also need a drill and a large diameter drill bit to create the hole for your finger. Sandpaper and/or a belt sander will be necessary to smooth and shape the wood, and you may also want to use a Dremel tool for more detailed sanding and shaping. If you want to add a finish to your ring, you will need oil such as Tung oil or linseed oil.
For a metal ring, you will need metalworking tools such as an extruder to shape the metal and a mandrel to form it into a circle. You will also need a hammer or mallet and a sanding surface to smooth and shape the ring. If you plan to set stones in the ring, you will need a torch to braze (or solder) the setting in place. You may also want to use a rotary tool or a Dremel tool for more detailed sanding and polishing.
In addition to these material-specific tools, there are some general tools that will be useful for making any type of wedding ring. These include a ring sizer to ensure a comfortable fit, a workshop or studio space to work in, and safety gear such as gloves and goggles to protect yourself during the ring-making process.
Remember that the specific tools you will need may vary depending on the design of your ring and the materials you choose. It is always a good idea to do some research and plan out the steps of your project before getting started.
Creating Fondant Flowers for Wedding Cakes: A Step-by-Step Guide
You may want to see also
Shaping the ring
Step 1: Choose the Right Wood
The first step is to select the appropriate wood for your ring. Since the ring will be thin, choose a dense and sturdy wood type. Examples include African Padauk, which has a deep orange or reddish colour that transforms into a warm brown over time when exposed to UV light, or Ipe, a Brazilian Walnut with a darker hue.
Step 2: Cut Out the Ring Blanks with the Grain
Respect the grain of the wood to avoid cracking the ring during the shaping process. Cut out the ring blanks from the billet so that the grain runs across it, not through it. Avoid trying to create a ring by cutting off the end of the wood, as this will likely result in cracking.
Step 3: Measure and Cut the Ring Blanks
Depending on the grain orientation of the billet, you can cut it into one long 3/8" strip and then into 1 3/8" size blocks, or cut multiple blocks at once from the end. Ensure you add extra width to account for the sanding process later.
Step 4: Drill the Hole
If you already have a ring, use a Speedbor or a drill bit slightly smaller than the ring's hole. If not, estimate the size, allowing for some adjustment later. Drill only halfway through, then flip the block over to prevent chipping. Go slowly and let the drill bit do the work.
Step 5: Sand the Hole to Fit
Use a Dremel tool to sand down the hole until it comfortably fits your finger. Remember, it should slide over your knuckle with ease.
Step 6: Freehand the Outer Diameter and Cut Off the Corners
Freehand the outer circle of the ring, or use a scribe if preferred. Cutting off the corners at this stage will save time during the sanding process.
Step 7: Sanding
This is a tedious and crucial step. Keep the ring moving if using a belt sander to avoid creating a flat spot. Sand the ring by hand for more control. Be cautious not to remove too much material, as it cannot be undone.
Step 8 (Optional): Heat Treat the Ring
Once the ring is close to its final shape, you can heat-treat it with a heat gun to strengthen the wood and create a unique burnt edge effect. Be careful not to overdo it, as too much heat can make the wood brittle.
Step 9 (Optional): Final Sanding and Oil Coating
You may choose to finish the ring with a final sanding step and a coat of oil, such as Tung oil. This step is optional, as the natural oils from your hands will coat the ring over time. However, exposure to certain detergents may remove this coating.
Making Friends at Weddings: A Guide to Mingling
You may want to see also
Adding stones or engravings
Type of Engraving
The most common types of engraving are either done by hand or by machine. Hand engraving is typically done using a handheld laser, while machine engraving is completed using a specialised machine and laser. Both methods are safe for your jewellery and will not harm the integrity of the ring. Machine engraving tends to be cheaper, while hand engraving is usually more expensive but adds a special handmade feel to the ring.
Timing
If you want your wedding ring engraving to be ready by the wedding, it is recommended to start the process at least two months in advance. However, if you decide to engrave your ring after the big day, it is still possible to do so at any time. Engraving can be done as quickly as while you wait or can take up to a month, depending on your jeweller.
Cost
The cost of engraving varies across jewellers, typically ranging from $35 to $100. The price usually depends on the number of characters in the inscription, the font used, and whether it is done by hand or machine. Some jewellers may charge a flat rate with no character limitations, while others may charge extra for additional characters.
What to Engrave
There are many options for what to engrave on a male wedding ring. Here are some ideas:
- Nicknames or initials
- Wedding date or engagement date
- A memorable quote or lyric
- A special moment or inside joke
- Religious or biblical verse
- A symbol, such as a heart or infinity symbol
- Coordinates of a special location, such as where you met or the wedding venue
Remember, there are no rules when it comes to engraving your wedding ring. You can choose something romantic, funny, or completely unique. Just make sure to keep it short and sweet, as most engravings are limited to 15-20 characters for men's rings.
Creating a Wedding Flower Basket: A Step-by-Step Guide
You may want to see also
Sizing and finishing
Sizing:
Firstly, determine the wearer's ring size. This step is vital to ensure the ring fits comfortably and securely. You can use a ring sizer or measure the circumference of the finger to determine the appropriate size. It's important to allow for some minor adjustments, as fingers can fluctuate in size depending on temperature and other factors.
Shaping:
Once you have the desired diameter, cut the metal to size. The ends should be flat, as you'll then need to bend the metal into an oval shape. This can be done using a male/female type machine, where the metal is placed between the two parts and cranked to achieve the desired curve. Repeat this process until you have an oval with ends that almost touch.
Joining:
To form a solid ring, braze the ends of the oval together. Use an oxy-acetylene torch to heat the metal until it glows red, then apply solder to create a strong joint. This step requires precision and control of the heat source to avoid overheating the metal.
Forming the Circle:
Now, it's time to transform the oval into a circle. Use a mandrel to hammer the ring into a circular shape, flipping it frequently to maintain symmetry. You can also use a manual press or a ring-compacting machine to achieve the desired size and shape. This process may take several attempts to get it just right.
Sanding:
Sanding is an important step to smooth out any rough edges and create a uniform surface. Use a flat sanding surface for the sides and a Dremel tool or rotary tool for the sides and interior. Be thorough, as this step ensures a comfortable fit and a polished appearance.
Finishing:
The final step is to polish the ring to achieve the desired finish. Depending on the chosen metal and style, you can opt for a matte, brushed, or high-shine finish. Use polishing tools and cloths designed for jewellery making to achieve the desired effect. Remember to polish both the inside and outside of the ring.
Creating a wedding ring is a meticulous process that requires patience and attention to detail. Taking your time with each step, especially sizing and finishing, will ensure a high-quality, durable ring that will be cherished for a lifetime.
Make Your Wedding Flourescently Lit Up
You may want to see also
Frequently asked questions
You can use a variety of materials, including gold, silver, platinum, tungsten, titanium, tantalum, cobalt, meteorite, Damascus steel, carbon fibre, and even wood or antler inlays.
Styles can include classic, minimal, and timeless designs with textured surfaces, matte, brushed, or polished finishes, and custom inscriptions.
The cost depends on the materials used and the design chosen. Male wedding rings can range from under $200 to over $8,500 for intricate diamond designs.
Gold and tungsten are popular choices, but you can also consider platinum, tantalum, cobalt, or titanium. Each metal has its own style and durability, so choose one that matches your style and budget.
The process typically involves picking the stones, metal, and sizing, designing the ring, and then casting or fabricating it. Fabrication may involve rolling, filing, soldering, and polishing, while casting involves carving a wax model and then casting it into metal.